Hot Melt vs. Cold Compaction Densifiers
Hot Melt
Densifiers
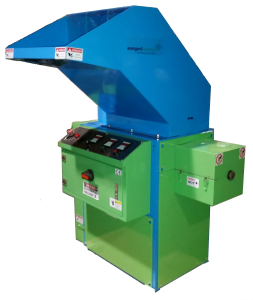
Hot melt densifiers are top fed via a hopper style infeed. Loose foam is dropped into the hopper where it goes through a shredding process. The shredded foam then drops down onto an auger which shuttles it into a melt unit.
The melt unit liquifies the foam and expels it out the side of the machine where it flows into a form mold that shapes the material into a block ideal for palletizing. Melt temperatures vary for each type of foam so the sophistication of the melt unit determines what types of foam each of our models can process.
As an example, the FD-10 is our entry level hot melt densifier and comes with a single temperature melt unit calibrated to melt EPS foam (more commonly known as Styrofoam) specifically. The FD-12 and subsequent models all come with multi temperature melt units capable of processing EPS, EPE and EPP.
Hot melt densifiers reduce foam volume at a ratio of 90:1.
Cold compaction densifiers are also top fed via a hopper. Loose foam is dropped into the hopper where it goes through a shredding process. The shredded foam then drops down onto an auger which shuttles it into a rectangular compaction chamber.
When the compaction chamber is full the auger stops turning and a hydraulic ram travels the length of the chamber compressing the air out of the foam.
The resultant densified material is pushed out of the machine in a continuous block shape which is then broken off at a length ideal for your pallet.
Cold compaction units densify EPS and PIR exclusively and reduce foam volume at a ratio of 60:1.
Cold Compaction Densifiers
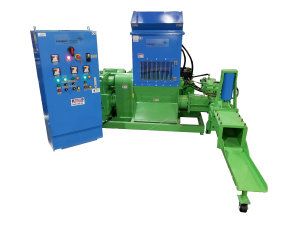
At Better Densifiers, we handle both hot melt and cold compaction foam densifiers. Each type utilizes different technology and each type offers unique advantages and benefits depending on the application.
Let’s talk through your project and get you the best and most cost-effective solution for your foam recycling needs. 1-800-350-2079